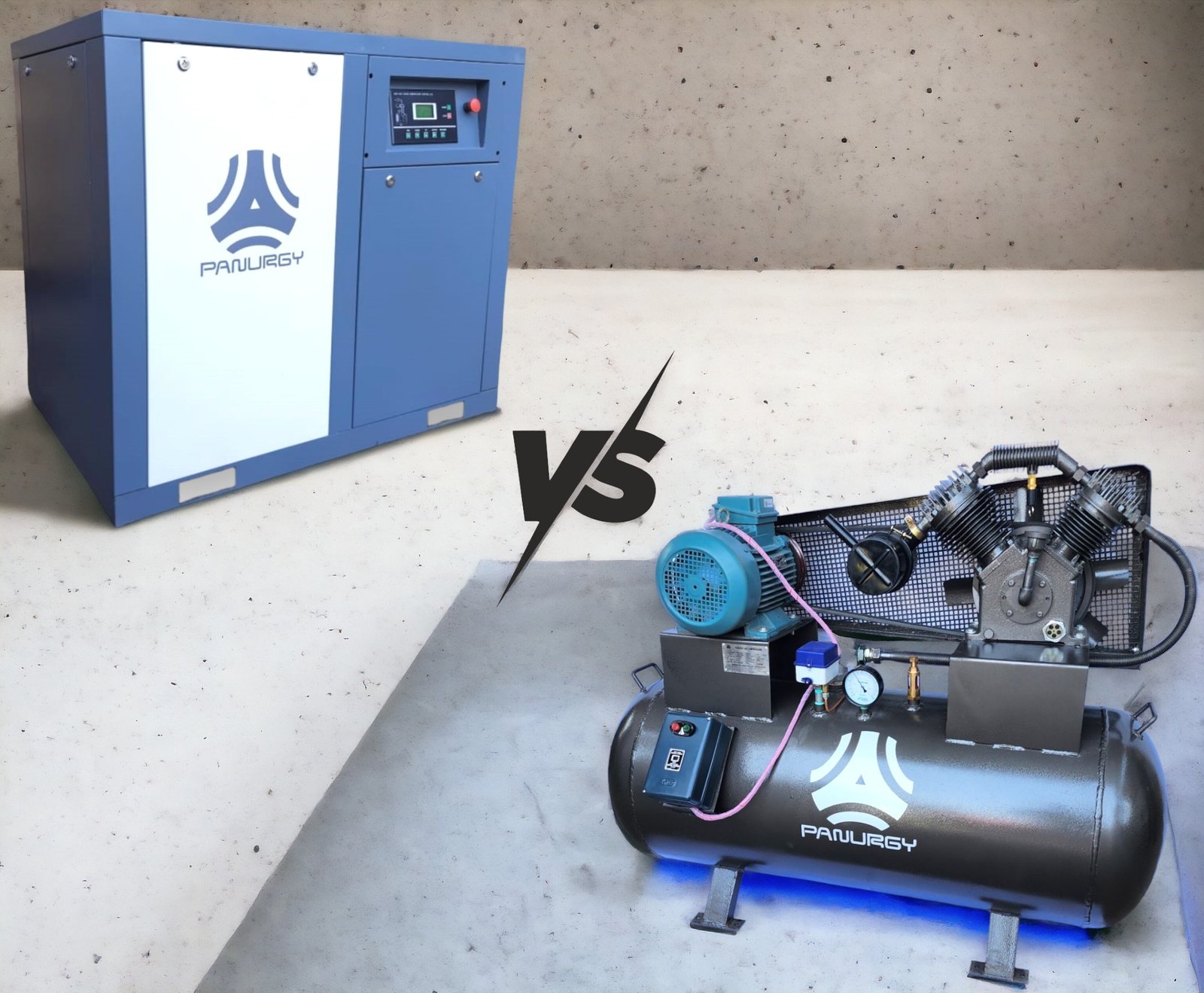
Screw Air Compressor vs Reciprocating Air Compressor: Differences & How to Choose Between the Two
When it comes to selecting an air compressor for your industrial or commercial application, the choice typically boils down to Screw Air Compressors and Reciprocating Air Compressors. Both types have distinct features, benefits, and drawbacks. Understanding these differences can help you make an informed decision tailored to your specific needs.
In this post, we will explore the key differences between screw and reciprocating compressors and provide guidance on how to choose the right compressor based on your application.
Screw Air Compressors: A screw air compressor uses twin rotating helical screws to compress air. As the screws rotate, the volume between them decreases, compressing the air and increasing its pressure. This continuous, rotary mechanism makes screw compressors ideal for high-demand, continuous operation environments.
Reciprocating Air Compressors: Reciprocating compressors, on the other hand, use pistons driven by a crankshaft to compress air. The piston moves back and forth within a cylinder, drawing air in on one stroke and compressing it on the next. These compressors are best suited for intermittent duty cycles where air demand fluctuates.
Screw Compressors: Screw compressors are designed for applications that require continuous operation, typically 100% duty cycle. This makes them the go-to choice for industries like manufacturing, pharmaceuticals, and automotive where air is needed 24/7.
Reciprocating Compressors: Reciprocating compressors have a lower duty cycle, typically around 60-70%, meaning they are better suited for applications where air is needed in short bursts or intermittently, such as in automotive workshops, small factories, or construction sites.
Screw Compressors: Screw compressors tend to be more energy-efficient in large-scale operations due to their continuous operation and minimal energy losses. They also offer Variable Frequency Drive (VFD) options, allowing you to adjust the compressor’s speed based on air demand, resulting in even greater energy savings.
Reciprocating Compressors: While reciprocating compressors are more affordable initially, they are less energy-efficient for large or continuous operations. Their stop-and-start nature can lead to higher energy consumption and more wear and tear.
Screw Compressors: Screw compressors generally require less frequent maintenance compared to reciprocating compressors due to fewer moving parts and their continuous operation design. Their components tend to be more robust, resulting in a longer lifespan in heavy-duty environments.
Reciprocating Compressors: Reciprocating compressors, with their pistons and valves, have more moving parts that are subject to higher wear and tear, especially in high-use applications. They require more frequent maintenance and downtime, particularly if used beyond their intended duty cycle.
Screw Compressors: Screw air compressors operate more quietly due to their smooth rotary motion, making them suitable for indoor use or environments where noise reduction is important.
Reciprocating Compressors: Due to the piston action, reciprocating compressors tend to be noisier, making them more suited to applications where noise levels aren’t a concern, such as construction sites or remote industrial locations.
Screw Compressors: Screw compressors are generally compact for the output they provide. They are available in smaller footprints with enclosed designs, which can fit well in factories or indoor facilities with limited space.
Reciprocating Compressors: Reciprocating compressors tend to be larger and bulkier relative to their air output, requiring more floor space. However, they are simpler in design, which can make them easier to install in various settings.
Screw Compressors: Screw compressors come with a higher upfront cost due to their advanced design and features. However, for businesses with continuous air demand, the lower operating and maintenance costs can result in significant savings over time.
Reciprocating Compressors: Reciprocating compressors are more affordable initially, making them attractive to smaller businesses or operations with low-to-moderate air demands. However, the increased maintenance costs and potential energy inefficiencies should be taken into consideration for long-term use.
How to Choose Between a Screw and Reciprocating Air Compressor?
1. Consider Your Application:
2. Duty Cycle and Operational Hours:
3. Energy Efficiency and Cost:
Conclusion
Both screw air compressors and reciprocating air compressors serve specific purposes in industrial and commercial applications. By understanding your operational needs, duty cycle requirements, and budget, you can choose the most appropriate compressor for your business. At Panurgy, we offer a wide range of both types to meet the diverse needs of our customers.
For more guidance or to request a quote, please get in touch with us today! To download our catalogue, please visit our website now!